Metal fabrication is an essential process across industries, turning raw metal into functional components and finished products.
From towering skyscrapers to delicate electronics, the machinery used in fabrication shapes the world we live in. But what tools make this transformation possible?
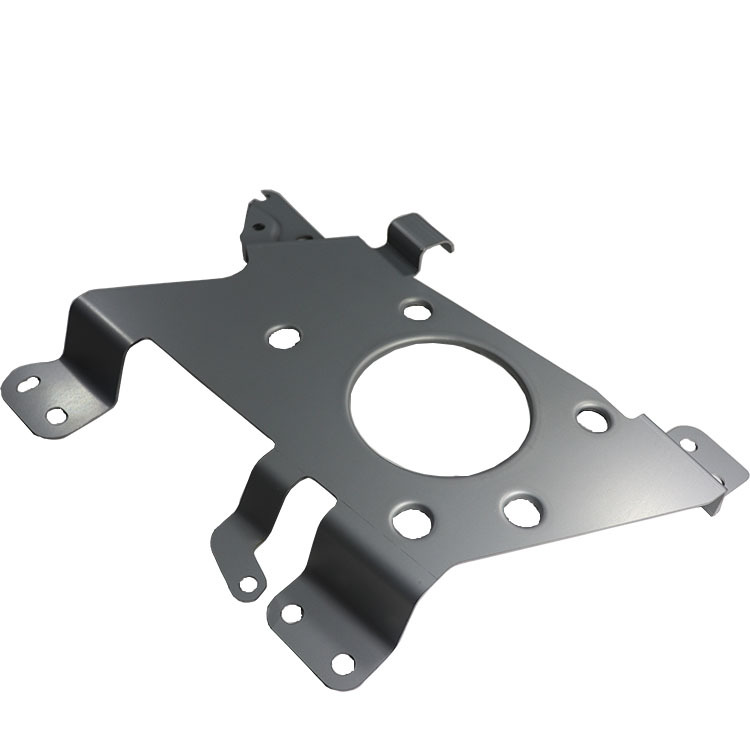
Metal fabrication relies on a variety of specialized machines, including lathes, milling machines, and welding equipment, each designed for specific tasks like cutting, shaping, and assembling metal.
These machines work together to ensure precision, efficiency, and durability in manufacturing. Understanding their functions is key to mastering the craft of metal fabrication.
So, now let’s explore the most commonly used equipment and their crucial roles in modern manufacturing.
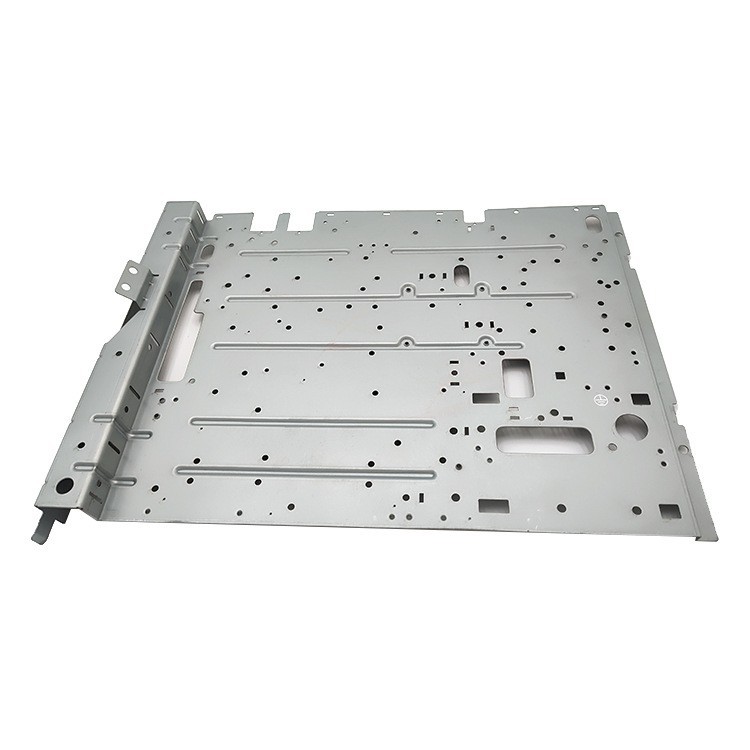
What Are the Key Machines in Metal Fabrication?
Metal fabrication machinery encompasses an array of tools designed to perform tasks such as cutting, bending, welding, and finishing.
These machines ensure precision, consistency, and efficiency in producing high-quality metal parts.
By utilizing the right equipment, businesses can meet specific industrial demands and achieve optimal results.
Learn more about our metal stamping services that leverage this technology.
Common Machines Used in Metal Fabrication
1. Lathe Machines
Lathe machines are among the oldest and most versatile tools in metalworking.
They rotate metal workpieces on their axis while cutting, shaping, or drilling. Lathes are indispensable for creating symmetrical parts like shafts, rings, and flanges, offering unparalleled precision.
2. Milling Machines
Milling machines use rotating cutting tools to shape metal.
They perform tasks such as drilling, slotting, and contouring, making them essential for creating detailed components. Whether for small or large parts, milling machines ensure accurate and efficient material removal.
3. Press Brakes
Press brakes bend sheet metal into precise shapes and angles using a punch-and-die system.
Modern CNC press brakes offer automated controls, improving accuracy and efficiency in high-volume production. They are widely used for manufacturing metal frames, enclosures, and structural components.
4. Shears
Shears provide a clean, distortion-free method for cutting sheet metal.
These machines are crucial in preparing metal for further processing, offering speed and precision. Mechanical, hydraulic, and pneumatic shears cater to different types and thicknesses of metal.
5. Plasma Cutters
Plasma cutters use a high-velocity jet of hot plasma to slice through conductive metals.
Known for their speed and precision, these machines are ideal for creating intricate designs in thick metal sheets, commonly used in automotive and construction industries.
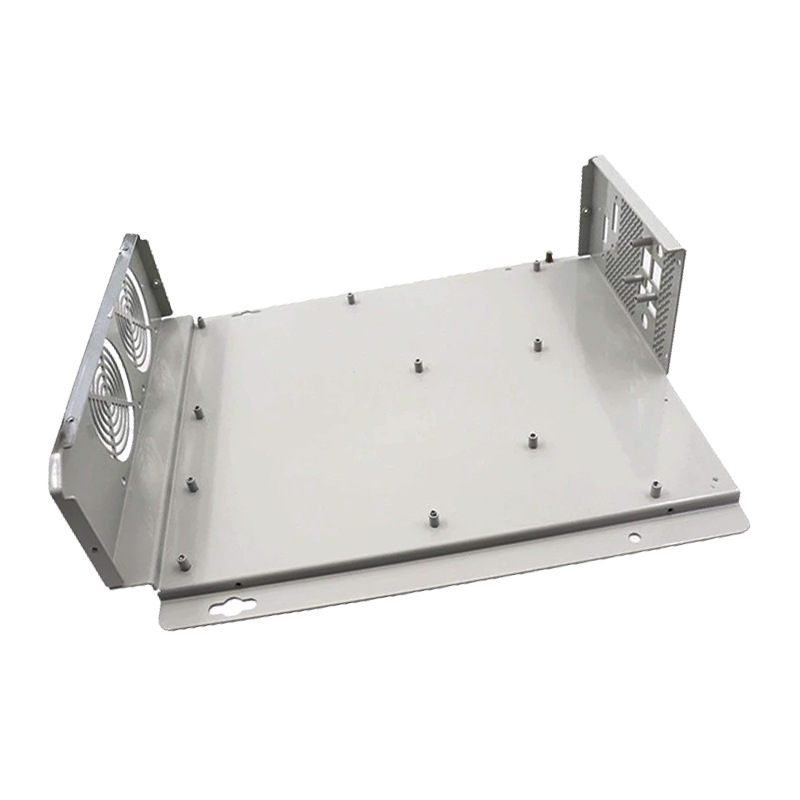
6. Waterjet Cutting Machines
Waterjet cutters use high-pressure water, often mixed with abrasives, to cut metals without generating heat.
This cold-cutting method is ideal for heat-sensitive materials, ensuring precision and preventing material distortion. Waterjet cutting is perfect for detailed designs and complex shapes.
7. Oxy-fuel Cutting Machines
Oxy-fuel cutters combine oxygen and fuel gas to cut through thick metal plates. They excel in heavy-duty applications like shipbuilding, large-scale construction, and industrial repair work.
8. Turret Punch Presses
Turret punch presses are ideal for mass production, punching shapes into metal sheets quickly and consistently.
With various punching tools housed in a rotating turret, this machine can produce multiple shapes in one operation, increasing efficiency and uniformity.
9. Welding Machines
Welding is a cornerstone of metal fabrication, and welding machines are indispensable for joining metal components.
MIG, TIG, and stick welding each serve different purposes. Robotic welding systems are gaining traction for their speed and precision in large-scale manufacturing.
10. Roll Forming Machines
Roll forming machines bend long strips of metal into continuous profiles.
These machines are commonly used in the construction industry to produce items like roofing panels, gutters, and structural reinforcements.
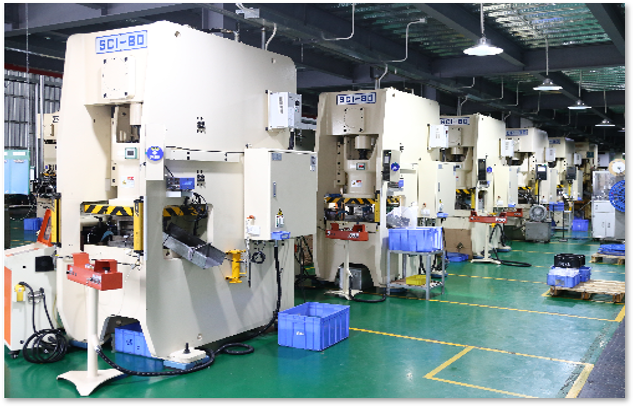
11. Tube Bending Machines
Tube benders shape metal tubes into precise angles without compromising their structural integrity.
These machines are essential in automotive, plumbing, and construction industries, where custom tubing designs are necessary.
12. Grinders
Grinders smooth and polish metal surfaces, removing imperfections and providing a professional finish.
They are typically used in the final stages of fabrication to enhance the product’s aesthetic and functional qualities.
13. Hydraulic Presses
Hydraulic presses exert immense force to bend, punch, or shape metal. They are ideal for creating heavy-duty parts, widely used in automotive, aerospace, and industrial machinery manufacturing.
14. Bandsaws
Bandsaws excel at cutting metal into precise shapes, including intricate curves and angles. Unlike shears, bandsaws can handle complex designs, making them essential for custom fabrication projects.
15. Finishing Equipment
Finishing equipment such as polishing machines, degreasers, and painting systems ensure that metal parts meet the required specifications. These tools improve the aesthetic and functional quality of fabricated products, preparing them for end-use.
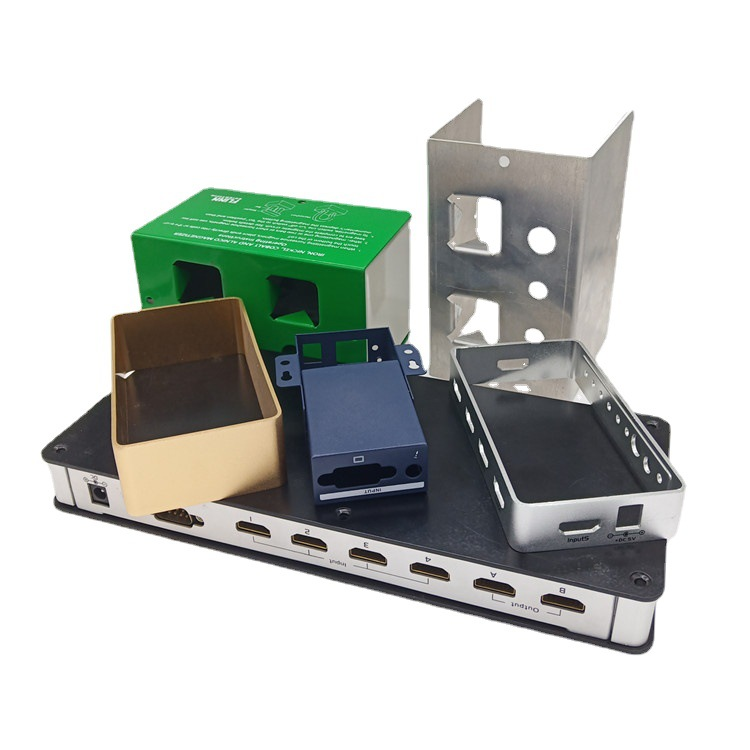
Why Automation is the Future of Metal Fabrication?
The rise of automation has revolutionized metal fabrication. CNC machines and robotic systems now dominate the industry, offering unparalleled precision and efficiency.
Automated machinery minimizes human error, increases production speed, and reduces labor costs.
Investing in automation is a game-changer for companies looking to scale operations, enabling them to handle more complex projects while maintaining consistency.
Industries from automotive to aerospace are leveraging these advanced machines to achieve unprecedented levels of precision.
By understanding how to design stamping dies, manufacturers can unlock new potential in their production processes.
How to Choose the Right Machinery for Your Needs?
Selecting the right machinery for your fabrication shop depends on your specific needs and production goals. Factors to consider include:
• Material Type and Thickness: Ensure the machines can handle the types and sizes of metal you work with.
• Production Volume: High-volume production may require CNC or automated machinery to meet demand efficiently.
• Precision Requirements: For industries like aerospace or electronics, precision is crucial. Opt for machines with high accuracy and advanced controls.
• Budget and Space: Evaluate your budget and available workspace before investing in new equipment.
Consulting with industry experts and conducting thorough research can help you make informed decisions.
Explore how advanced materials and cutting-edge machinery can revolutionize your production process. Contact Partzcore today for a personalized consultation!
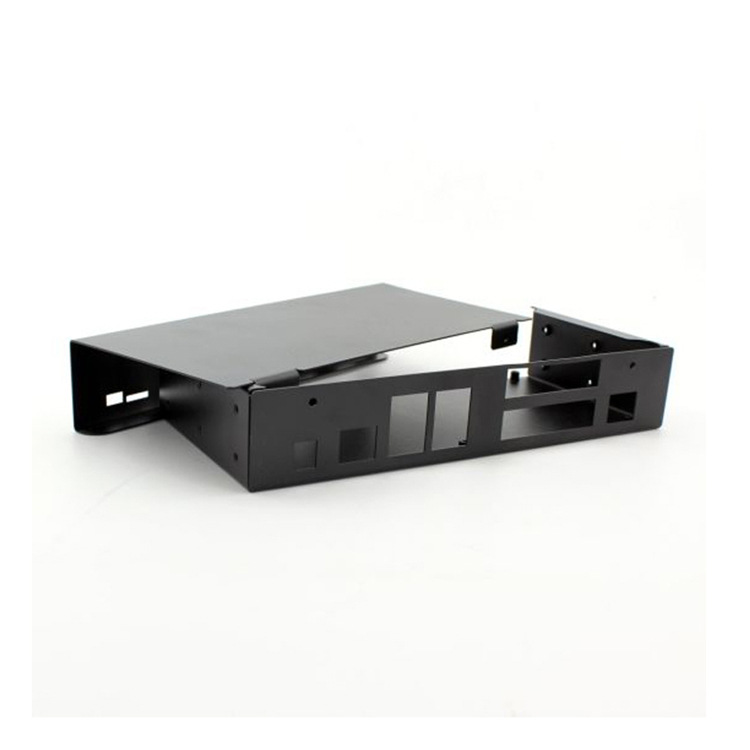
Conclusion
Metal fabrication machinery is the backbone of modern manufacturing, enabling the production of everything from small components to massive industrial structures.
Each machine plays a specific role in the fabrication process, contributing to the precision and durability of the final product.
With advancements in automation and maintenance practices, the future of metal fabrication is poised for greater efficiency and innovation.
Whether you’re new to the field or a seasoned professional, understanding and utilizing the right tools will ensure long-term success in this dynamic industry.