Aluminum anodizing is a critical process in various industries, enhancing the metal’s durability and aesthetic appeal.
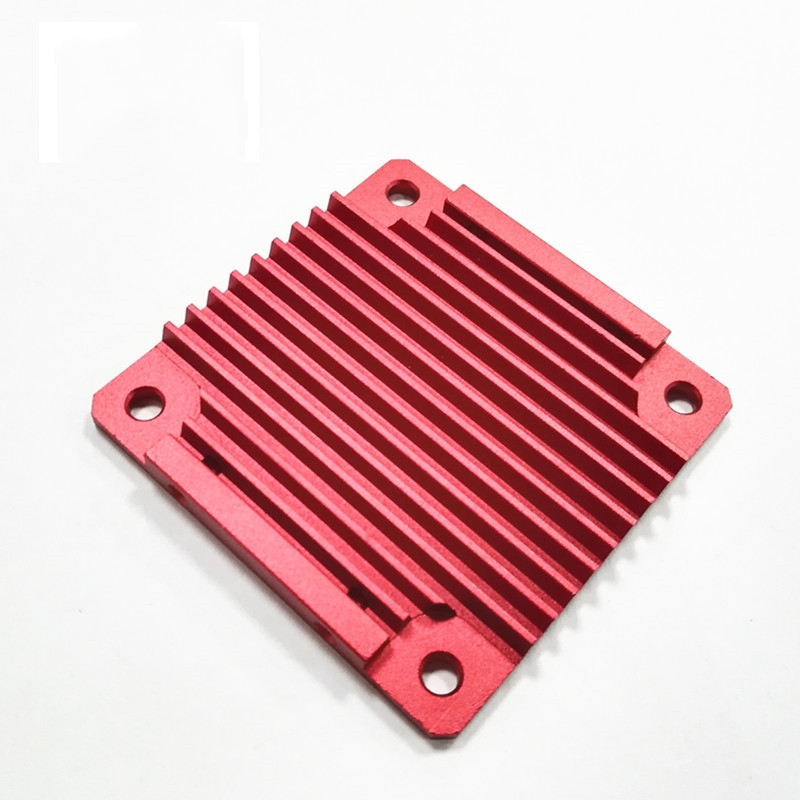
Aluminum anodizing is an electrolytic process used to increase the thickness of the tightly adhering oxide layer that forms naturally on any aluminum surface exposed to air.
The anodized layer has a porous, ordered structure that improves durability and corrosion resistance.
The anodizing process involves several steps, including cleaning, etching, anodizing, and sealing, each of which plays a crucial role in achieving the desired properties of the anodized aluminum.
Next, we will comprehensively delve into the intricacies of aluminum anodizing, providing valuable insights for industry professionals, engineers, production managers, and customers. Understanding aluminum anodizing is essential for making informed decisions in manufacturing and product development.
-
Table Of Contents
-
1. Everything You Need to Know About Aluminum Anodizing
-
2. Why Do We Need Aluminum Anodizing?
-
3. Where is Anodized Aluminum Used?
-
4. How Does Aluminum Anodizing Work?
-
5. How to Tell if Aluminum is Anodized
-
6. What are the Types of Aluminum Anodizing Processes?
-
7. What are the Benefits of Aluminum Anodizing?
-
8. What are the Materials Needed to Anodize Aluminum?
-
9. What are the Anodizing Colors for Aluminum?
-
10. How Long Will Anodized Aluminum Last?
-
11. Is Anodized Aluminum Prone to Rust?
-
12. Summary
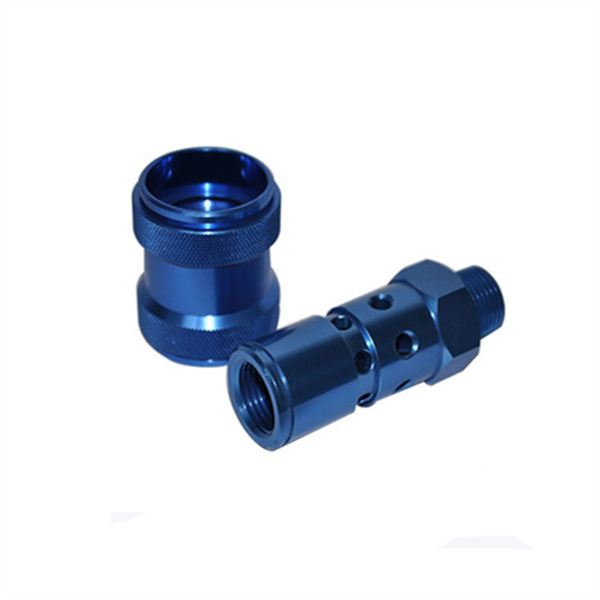
Why Do We Need Aluminum Anodizing?
The primary purpose of aluminum anodizing is to protect the metal from environmental damage and wear.
By increasing the thickness of the oxide layer, anodizing provides a robust barrier against corrosion, scratches, and other physical damage.
Additionally, anodizing improves the metal’s appearance, making it suitable for both functional and decorative applications.
This enhanced durability makes anodized aluminum an ideal material for products exposed to harsh environments, such as marine equipment, architectural elements, and automotive parts.
Where is Anodized Aluminum Used?
Anodized aluminum is used in a wide range of industries, including aerospace, automotive, electronics, and construction.
Its enhanced durability and aesthetic versatility make it ideal for components that require both strength and visual appeal.
Common applications include aircraft parts, automotive trim, architectural structures, and consumer electronics.
In the aerospace industry, anodized aluminum is used for structural components due to its lightweight and high strength-to-weight ratio.
In the automotive sector, it is used for exterior trim and interior accents, providing a durable and attractive finish.
How Does Aluminum Anodizing Work?
The anodizing process involves immersing the aluminum in an electrolytic solution, typically sulfuric acid. An electrical current is passed through the solution, causing the aluminum to oxidize and form a thick, porous oxide layer.
This layer can then be sealed to increase corrosion resistance and dyed to achieve the desired color. The anodizing process can be divided into several steps:
1. Cleaning: The aluminum surface is thoroughly cleaned to remove any contaminants that could affect the anodizing process.
2. Etching: The aluminum is etched in an acidic solution to create a uniform surface.
3. Anodizing: The aluminum is placed in an electrolytic bath, and an electric current is applied, causing the oxide layer to form.
4. Sealing: The porous oxide layer is sealed by immersing the aluminum in boiling water or a chemical solution, closing the pores and enhancing corrosion resistance.
Each step in the process is carefully controlled to ensure the quality and consistency of the anodized finish.
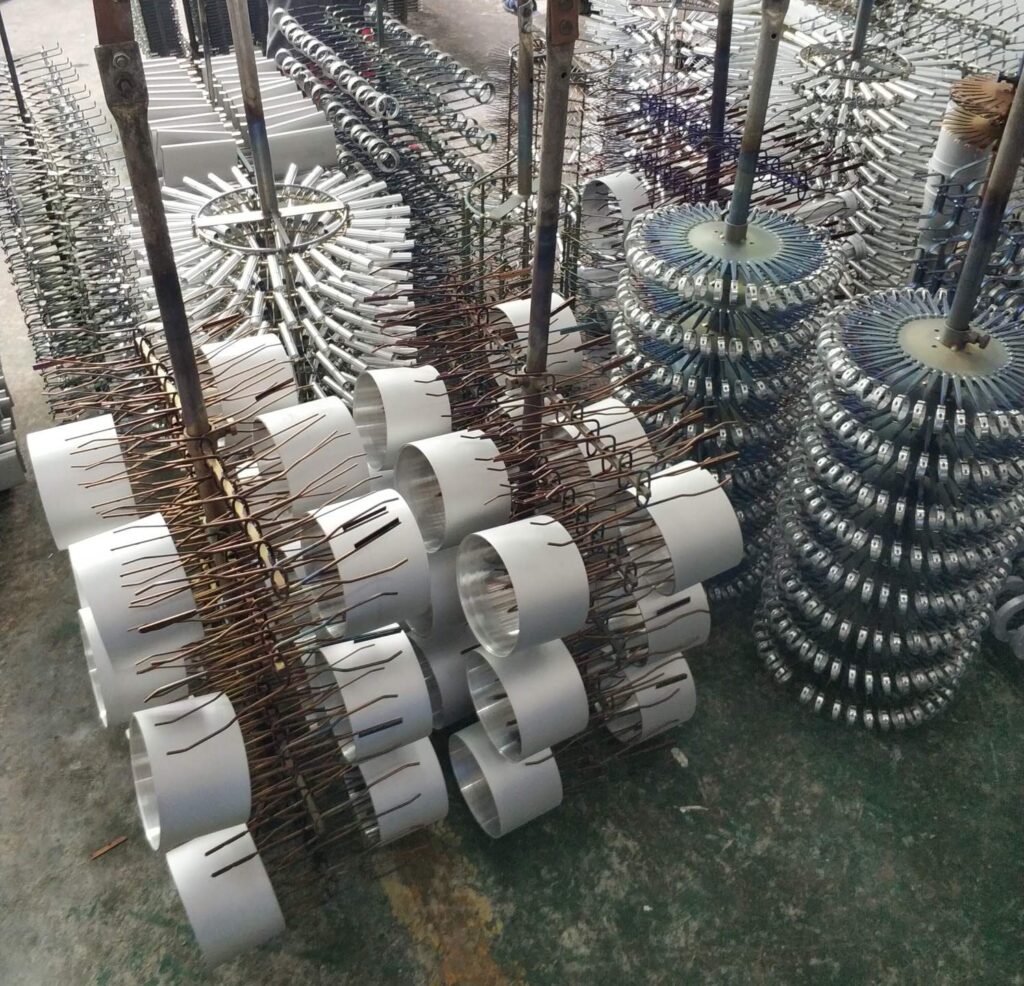
How to Tell if Aluminum is Anodized
You can determine if aluminum is anodized by inspecting its surface.
Anodized aluminum typically has a matte finish and may appear slightly darker than non-anodized aluminum.
Additionally, anodized aluminum is more resistant to scratching and corrosion.
A simple test involves scratching the surface; anodized aluminum will show less damage compared to non-anodized aluminum.
Another method is to apply a drop of nitric acid to the surface; if the aluminum is anodized, the acid will not react with the oxide layer.
What are the Types of Aluminum Anodizing Processes?
There are several types of aluminum anodizing processes, each with unique characteristics:
1. Type I (Chromic Acid Anodizing): This type uses chromic acid as the electrolyte and offers excellent corrosion resistance. It is less likely to cause dimensional changes in the metal, making it suitable for precision parts.
2. Type II (Sulfuric Acid Anodizing): The most common type, providing good corrosion resistance and the ability to be dyed in various colors. This process uses sulfuric acid as the electrolyte and is widely used for both decorative and functional applications.
3. Type III (Hard Anodizing): Also known as hard coat anodizing, this type produces a thicker, more durable oxide layer. It is suitable for applications requiring extreme wear resistance, such as in mechanical components and heavy-duty equipment.
Each type of anodizing offers different benefits and is chosen based on the specific requirements of the application.
What are the Benefits of Aluminum Anodizing?
Aluminum anodizing offers numerous benefits, including:
• Enhanced Corrosion Resistance: The anodized layer protects the aluminum from environmental factors, preventing rust and corrosion.
• Increased Surface Hardness: Anodized aluminum is significantly harder than untreated aluminum, making it more resistant to scratches and wear.
• Improved Wear Resistance: The anodized layer provides a durable surface that withstands friction and abrasion.
• Aesthetic Versatility: Anodized aluminum can be dyed in various colors, allowing for a wide range of design possibilities.
• Environmentally Friendly Process: Anodizing is a relatively low-impact process, and the resulting oxide layer is non-toxic and does not emit harmful substances.
These benefits make anodized aluminum a preferred material in many industries, providing both functional and aesthetic advantages.
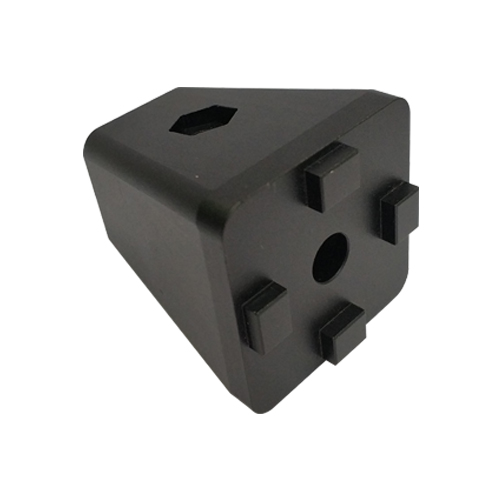
What are the Materials Needed to Anodize Aluminum?
To anodize aluminum, the following materials are required:
• Sulfuric Acid: Used as the electrolyte in the anodizing bath.
• Distilled Water: To dilute the sulfuric acid and for rinsing the aluminum.
• Several Tanks (Containers): To hold the different solutions used in the anodizing process.
• A Cathode: Typically made of aluminum or lead, used to complete the electrical circuit in the anodizing bath.
• Aluminum Wire: Used to suspend the aluminum parts in the anodizing bath (titanium wire can also be used).
• Degreaser: To clean the aluminum surface before anodizing.
• Lye (Sodium Hydroxide): Used to etch the aluminum surface.
• Acid Neutralizer: To neutralize any remaining acid on the aluminum after anodizing.
Proper preparation and handling of these materials are essential for achieving a high-quality anodized finish.
What are the Anodizing Colors for Aluminum?
Anodized aluminum can be dyed in a wide range of colors, including black, blue, red, gold, and green.
The dye is absorbed into the porous oxide layer, resulting in a vibrant and durable finish. Custom colors can also be achieved by mixing different dyes.
The ability to dye anodized aluminum in various colors makes it a versatile material for decorative applications, such as in architectural elements, consumer electronics, and automotive trim.
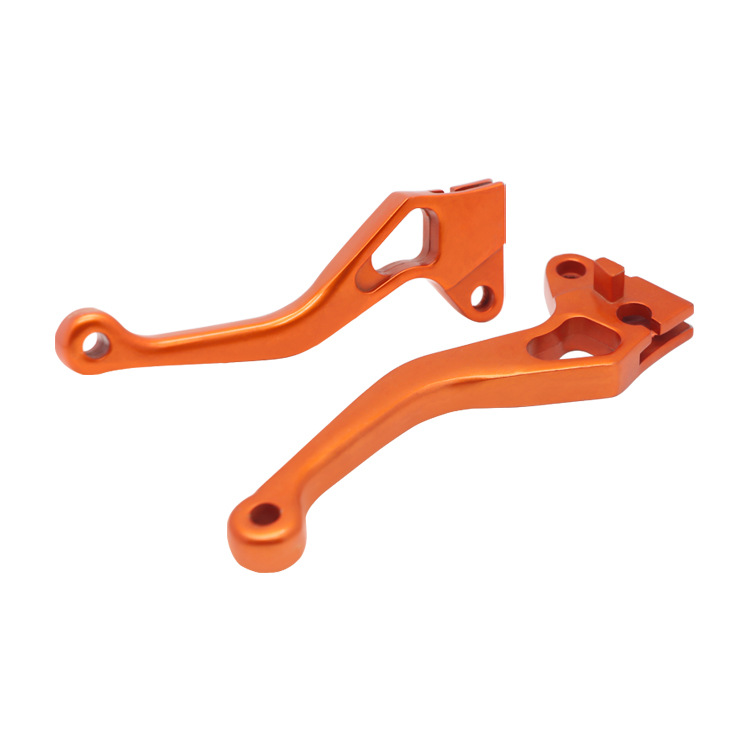
How Long Will Anodized Aluminum Last?
The lifespan of anodized aluminum depends on the thickness of the oxide layer and the conditions it is exposed to.
In general, anodized aluminum can last for decades without significant degradation. Proper sealing and maintenance can further extend its longevity.
Anodized aluminum used in outdoor applications, such as building facades and window frames, can maintain its appearance and performance for 20 to 30 years or more.
Indoor applications, where the aluminum is less exposed to harsh environmental conditions, can last even longer.
Is Anodized Aluminum Prone to Rust?
Anodized aluminum is not prone to rust, as aluminum oxide forms a protective barrier that prevents oxidation and corrosion.
Unlike iron, aluminum does not rust when exposed to moisture and air.
The anodized layer enhances this natural resistance, making it an excellent choice for outdoor and marine applications.
The anodized layer acts as a barrier that prevents moisture and oxygen from reaching the underlying aluminum, ensuring long-lasting protection against corrosion.
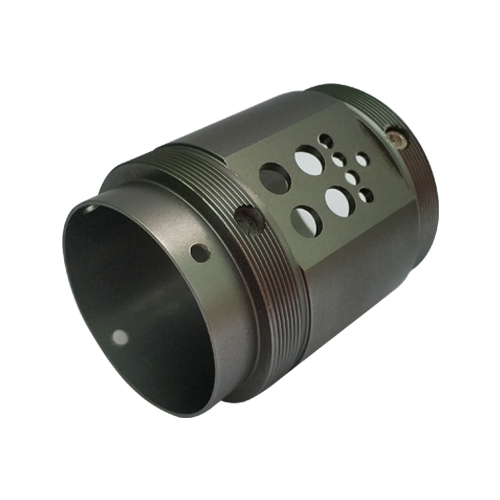
Summary
In conclusion, aluminum anodizing is a vital process that enhances the durability, appearance, and corrosion resistance of aluminum.
Understanding the different types of anodizing processes, their benefits, and applications can help industry professionals make informed decisions.
Whether for functional or decorative purposes, anodized aluminum offers a reliable and aesthetically pleasing solution. With its wide range of applications and numerous benefits, aluminum anodizing continues to be an essential process in various industries.