In the world of aluminium die casting, surface quality is paramount.
Among the most overlooked yet potentially serious imperfections are ejector pin marks—small circular impressions left behind when the casting is ejected from the mold.
While often dismissed as cosmetic blemishes, could these marks actually lead to deeper structural problems?
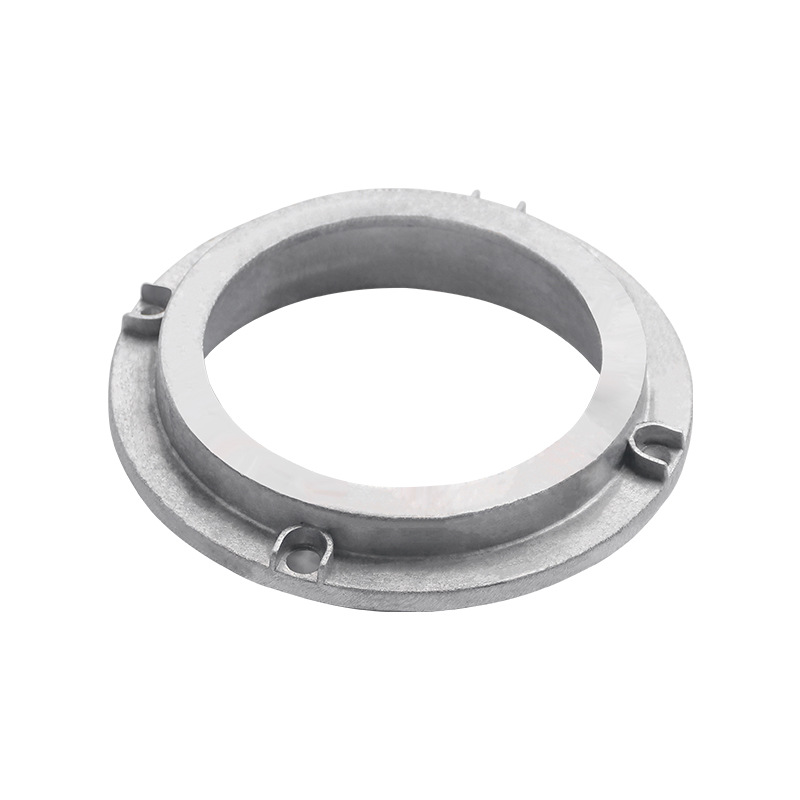
The short answer is yes.
Ejector pin marks can become stress concentrators that trigger cracks or mechanical failure, especially in high-stress or load-bearing components.
Poor mold design, excessive injection pressure, uneven cooling, and improper ejection techniques all increase the risk of deeper marks that compromise the durability and performance of die cast parts.
In this article, let’s dive deeper into how ejector pin marks form, why they matter, and—most importantly—what manufacturers can do to prevent them from becoming costly defects.
-
Table Of Contents
-
1. Can Ejector Pin Marks Really Cause Structural Defects in Die Cast Parts?
-
2. What Are Ejector Pin Marks and Why Do They Matter?
-
3. What Causes Ejector Pin Marks in Aluminium Die Casting?
-
4. How Can Ejector Pin Marks Lead to Structural Defects?
-
5. How Does Mold Design Help Prevent Ejector Pin Mark-Related Defects?
-
6. Why Is Injection Pressure Control Important?
-
7. What Impact Does Cooling Have on Ejector Pin Marks?
-
8. Can Mold Release Agents Help Reduce Ejector Pin Marks?
-
9. How to Detect and Address Potential Structural Defects?
-
10. Summary
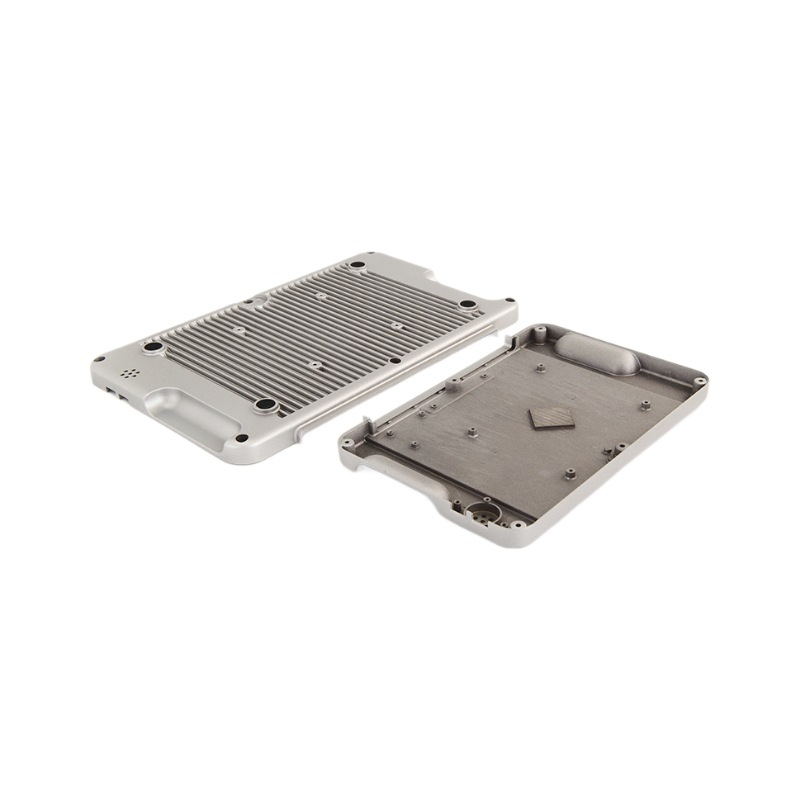
What Are Ejector Pin Marks and Why Do They Matter?
Ejector pins are essential in die casting molds.
After molten aluminium solidifies within the mold cavity, these pins push the cooled part out for the next cycle.
However, when these pins contact the part’s surface, they can leave slight indentations or raised marks known as ejector pin marks.
In many cases, these marks are purely aesthetic and can be polished away.
However, in critical applications—such as automotive, aerospace, or structural components—these small imperfections can have outsized consequences.
Deep ejector pin marks can serve as stress risers, where mechanical stress concentrates during use.
This increases the likelihood of microcracks forming and propagating, ultimately leading to part failure under load or fatigue conditions.
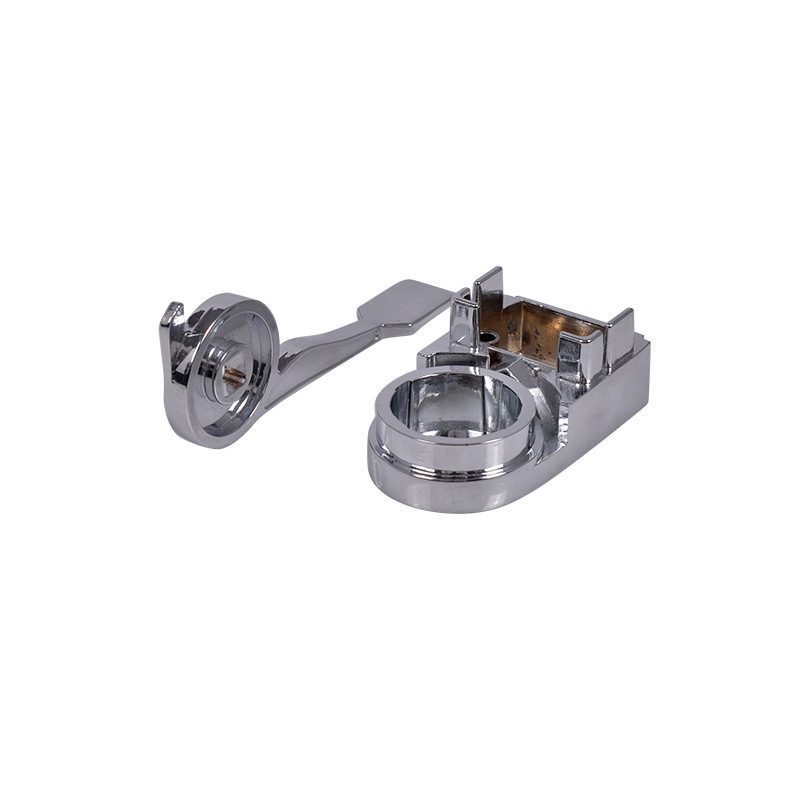
What Causes Ejector Pin Marks in Aluminium Die Casting?
Ejector pin marks result from several interconnected factors, including:
• Excessive Ejection Force: If the part sticks to the die, a higher ejection force is required, increasing the depth and severity of pin marks.
• Insufficient Draft Angles: Without adequate draft, the part clings to the die walls, making smooth ejection difficult.
• Uneven Cooling: Areas of the part may cool and shrink at different rates, causing localized gripping that requires more force to release.
• High Injection Pressure: Excessive pressure can force molten aluminium into tiny gaps around the pins, creating flash and more pronounced marks.
• Pin Geometry and Placement: Sharp or poorly placed ejector pins can leave deeper and more visible impressions.
Each of these factors can independently or collectively lead to surface marks that, if located in high-stress zones, can initiate fatigue cracks.
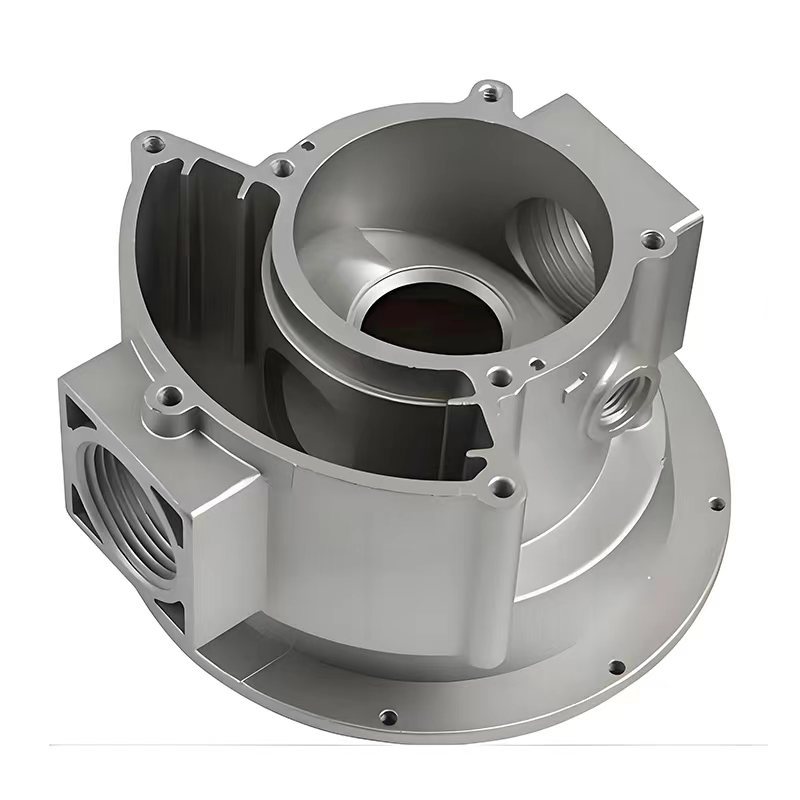
How Can Ejector Pin Marks Lead to Structural Defects?
Ejector pin marks, especially if deep, act as geometric discontinuities that concentrate mechanical stress.
These stress concentrators are well-known triggers for crack initiation in metals.
Under cyclic loading—such as vibration, bending, or thermal expansion—microcracks can develop from these marks, gradually propagating until catastrophic failure occurs.
The risk is highest in applications where:
• The component experiences dynamic loading (e.g., engine parts, brackets, transmission housings).
• The part has thin walls or minimal material thickness.
• The component is made from alloys with lower ductility or higher brittleness.
For example, in aluminium-silicon alloys commonly used in die casting, even small surface defects can significantly reduce fatigue life.
This makes controlling ejector pin marks not just a matter of cosmetic perfection but of ensuring structural integrity.
How Does Mold Design Help Prevent Ejector Pin Mark-Related Defects?
A well-designed mold is the most powerful tool in preventing ejector pin marks that could compromise part performance. Key mold design strategies include:
• Optimal Pin Placement: Position ejector pins in low-stress, non-cosmetic areas whenever possible. Avoid thin-walled regions and load-bearing zones.
• Balanced Ejection System: Ensures that all pins push simultaneously and evenly, preventing localized stress.
• Pin Diameter and Tip Shape: Larger pins distribute the load over a wider area. Radiused or polished tips help minimize surface marking.
• Adequate Draft Angles: Sufficient draft makes ejection easier and reduces the need for high pin forces.
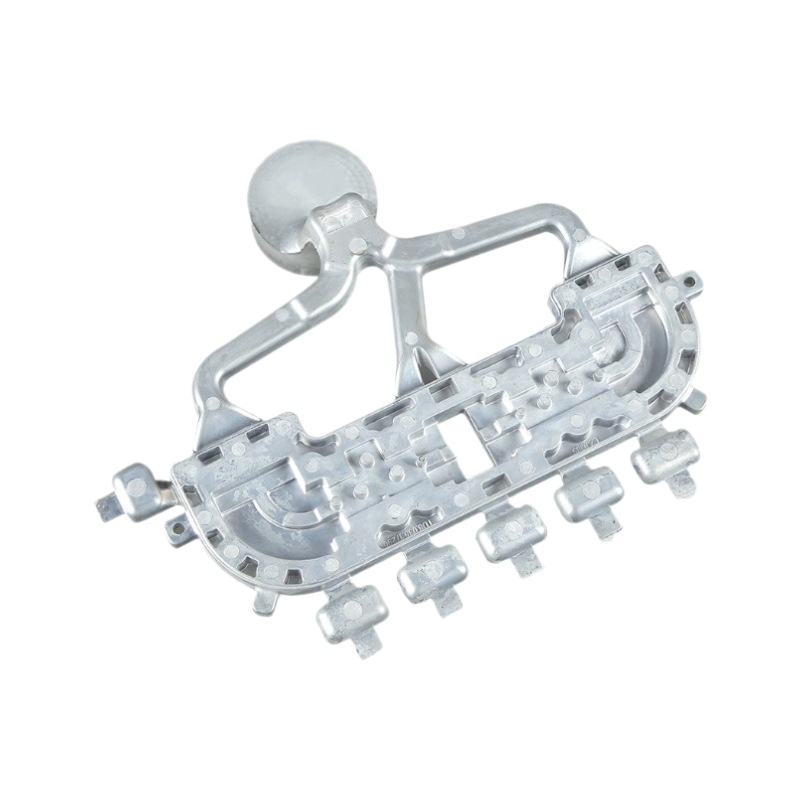
Why Is Injection Pressure Control Important?
Injection pressure in die casting is a delicate balance.
High pressure ensures rapid filling of complex cavities but can also exacerbate surface defects if not properly controlled.
Excessive injection pressure can:
• Force metal into ejector pin clearances, creating flash or exaggerated pin marks.
• Increase die wear, making sticking more likely over time.
Process optimization through multi-stage injection profiles allows manufacturers to reduce peak pressures without compromising fill quality.
This not only minimizes ejector pin marks but also extends tool life.
What Impact Does Cooling Have on Ejector Pin Marks?
Consistent and balanced cooling is critical to both part quality and defect prevention.
Uneven cooling leads to differential shrinkage, which:
• Causes the part to grip the mold inconsistently, requiring higher ejection forces.
• Results in internal stress that may amplify the effects of any surface imperfections, including ejector pin marks.
Designing effective cooling channels and using thermal control systems help maintain uniform temperatures across the die.
This not only prevents marks but also reduces internal stress, warping, and dimensional variations.
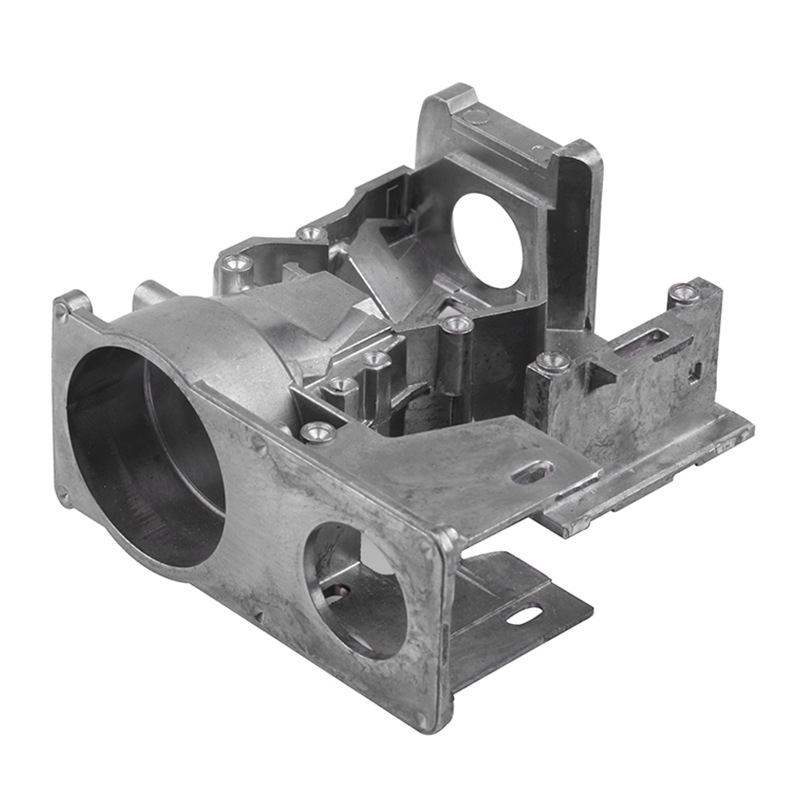
Can Mold Release Agents Help Reduce Ejector Pin Marks?
Proper application of mold release agents significantly reduces sticking, allowing parts to eject with less force.
However, overuse or uneven application can introduce other defects, such as blistering or incomplete filling.
Best practices include:
• Applying the right amount of release agent uniformly.
• Selecting lubricants that match the alloy and casting conditions.
• Monitoring spray intervals and coverage for consistency.
Combined with good mold design, proper use of mold release agents ensures smoother ejection and cleaner surfaces.
How to Detect and Address Potential Structural Defects?
Even with optimized design and process control, inspection remains crucial.
Visual inspections can catch obvious ejector pin marks, but for critical parts:
• Dye Penetrant Testing: Reveals surface-breaking cracks.
• X-ray or CT Scanning: Detects internal flaws or voids related to ejection marks.
• Fatigue Testing: Verifies whether surface imperfections influence long-term durability.
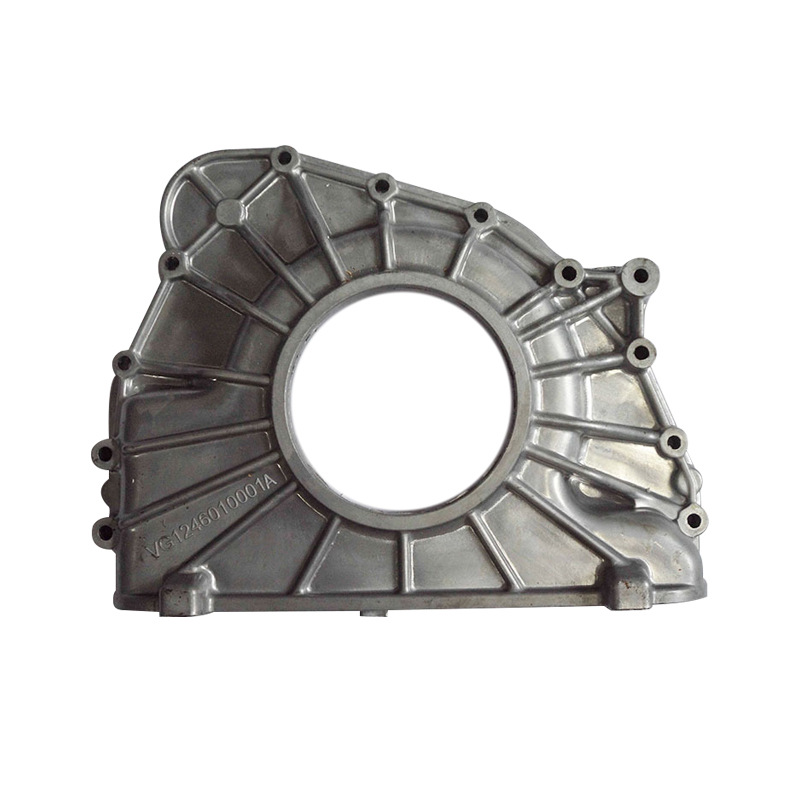
Conclusion:
While ejector pin marks in aluminium die casting are often seen as minor surface imperfections, their potential to trigger structural defects cannot be underestimated.
In high-performance or safety-critical applications, even small marks can act as stress concentrators, leading to fatigue cracks, premature failure, or costly recalls.
By focusing on precision mold design, balanced cooling, controlled injection pressure, and proper use of mold release agents, manufacturers can greatly reduce or eliminate ejector pin marks.
Additionally, rigorous inspection and testing help ensure that no hidden defects escape into the supply chain.
For businesses committed to delivering defect-free die cast components, controlling every step of the process is essential to maintaining both quality and customer trust.