Aluminium die casting is a widely used process for producing complex, high-precision components.
But can this process handle parts with varying wall thicknesses without sacrificing quality?
This question is especially important for industries where lightweight designs and mechanical strength must go hand in hand.
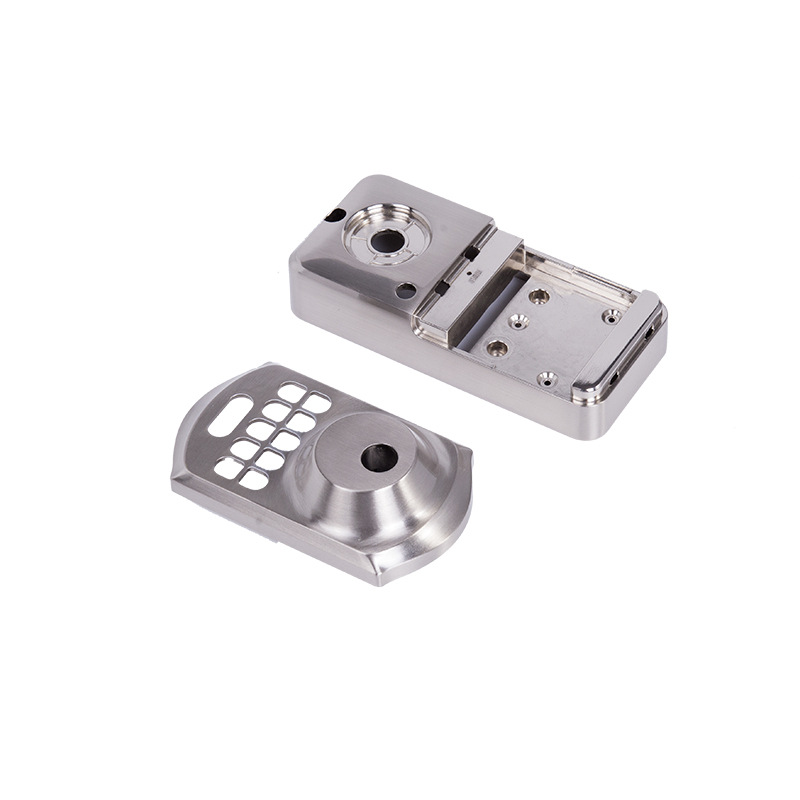
Aluminium die cast parts can feature varying wall thicknesses, but careful design and process control are essential.
Abrupt changes in thickness can cause serious casting defects such as shrinkage, porosity, and warping, primarily due to uneven metal flow and inconsistent cooling.
Manufacturers must prioritize gradual transitions, proper support structures, and process optimization to maintain part integrity and appearance.
When done correctly, die casting offers the flexibility to produce components with functional variations while ensuring strength and reliability.
Now, let’s explore in depth how wall thickness affects aluminium die casting and how expert design can overcome its challenges.
-
Table Of Contents
-
1. Can Aluminium Die Cast Parts Have Varying Wall Thicknesses?
-
2. Why Might Die Cast Parts Need Varying Wall Thicknesses?
-
3. What Challenges Do Wall Thickness Variations Introduce?
-
4. How Does Wall Thickness Affect Molten Metal Flow?
-
5. What Is the Impact on Cooling and Solidification?
-
6. How Do Ribs and Fillets Help Manage Thickness Variations?
-
7. Can Die Casting Handle Sudden Wall Thickness Changes?
-
8. What Design Strategies Ensure Successful Thickness Variations?
-
9. How Do Process Controls Support Quality in Parts with Varying Thickness?
-
10. Summary

Why Might Die Cast Parts Need Varying Wall Thicknesses?
In real-world applications, uniform wall thickness isn’t always possible. Design requirements often dictate thicker sections in areas where parts must:
• Bear mechanical loads or impacts
• Accommodate threads, bosses, or inserts
• House internal channels for cooling or fluid passage
• Feature aesthetic elements such as logos or design accents
Automotive and electronics industries, for example, frequently rely on aluminium die casting for components with complex geometries and varying wall thicknesses.
To meet these needs without introducing quality risks, design flexibility and process constraints must be balanced.
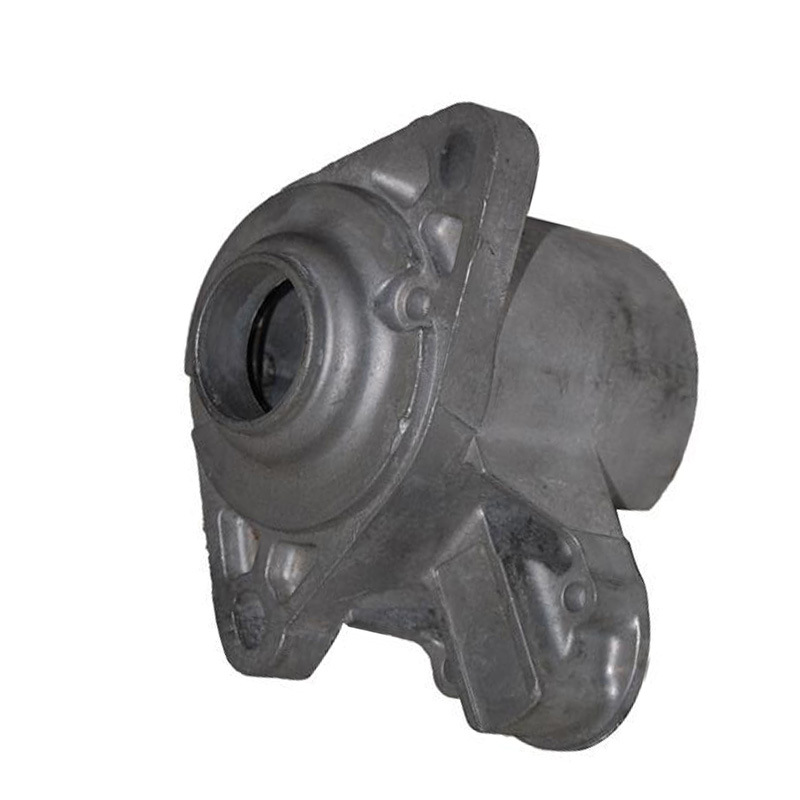
What Challenges Do Wall Thickness Variations Introduce?
While varying wall thicknesses may be unavoidable, they introduce several manufacturing challenges:
• Metal Flow Issues: Thicker sections can slow down the flow of molten aluminium, causing incomplete filling or cold shuts in thinner areas.
• Cooling Imbalances: Thicker areas cool slower than thin sections, creating internal stress, warping, or cracking.
• Shrinkage and Porosity: Thick zones solidify last, increasing the risk of shrinkage cavities or gas entrapment that weakens structural integrity.
Without careful planning, these defects can compromise both the mechanical properties and appearance of the final part.
That’s why manufacturers use advanced simulation tools and design techniques to mitigate these risks before production begins.
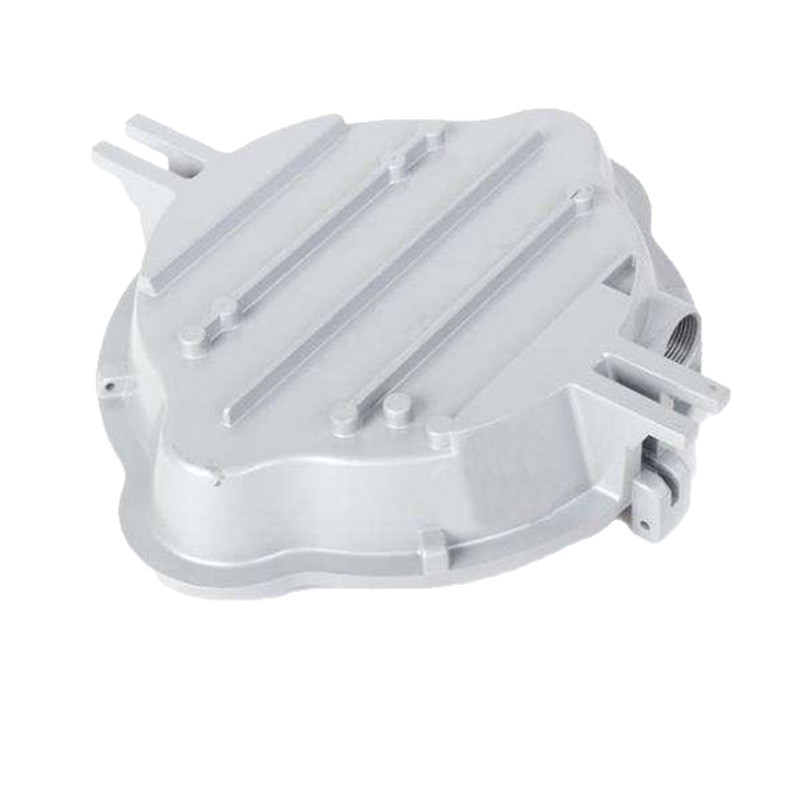
How Does Wall Thickness Affect Molten Metal Flow?
Molten aluminium in die casting must flow quickly and consistently through the mold cavity.
Uneven wall thickness creates:
• Fast-cooling thin sections that can solidify before the mold is fully filled, leading to misruns or cold shuts.
• Slower-filling thick sections that act as flow barriers, causing turbulence and trapped air.
Proper gating and runner design ensures that molten metal fills the entire mold evenly.
Multi-gate approaches, overflow wells, and strategically placed vents also help control flow direction and speed.
What Is the Impact on Cooling and Solidification?
Varying wall thickness directly impacts how parts cool and solidify:
• Thin sections cool faster, creating fine-grained, high-strength material with minimal shrinkage.
• Thicker sections cool slower, increasing the chance of porosity, shrink marks, and uneven microstructure.
This mismatch in cooling rates can create residual stress, leading to warping or cracking during ejection or later in service. Solutions include:
• Designing balanced cooling channels in the die
• Using targeted cooling near thicker areas
• Controlling mold temperature consistently across cycles
Simulation software helps visualize heat distribution, allowing designers to make informed adjustments before tooling is built.
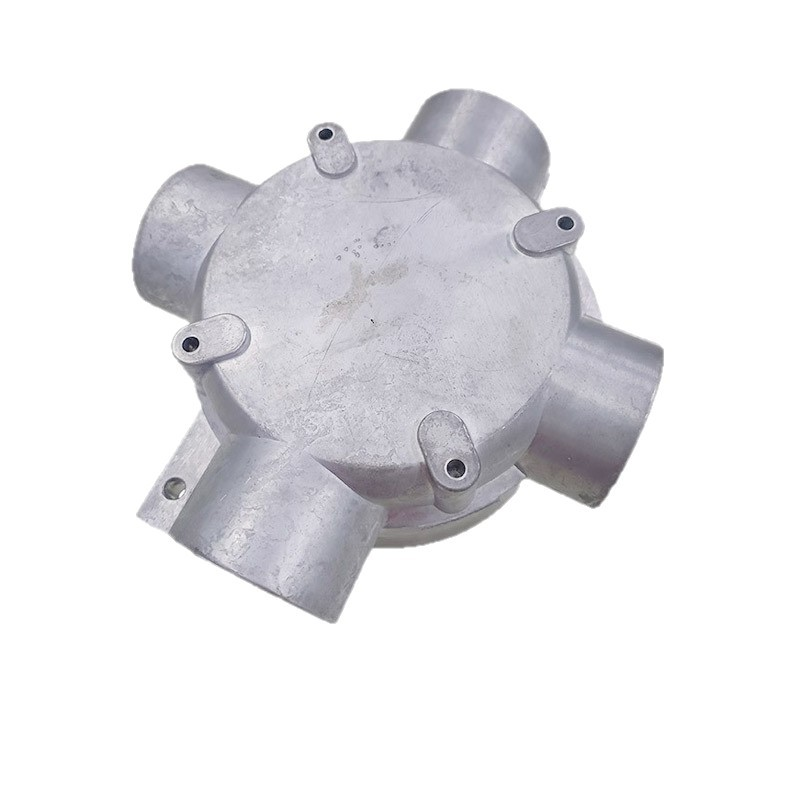
How Do Ribs and Fillets Help Manage Thickness Variations?
Adding material to increase strength is not always the best approach. Instead of thickening walls, incorporating ribs can:
• Improve stiffness without adding weight
• Reduce warping by promoting even cooling
• Avoid excessive material cost
Fillets serve a different but equally vital role:
• Eliminate sharp corners that concentrate stress
• Encourage smooth metal flow during filling
• Distribute heat evenly during solidification
Together, ribs and fillets help designers manage varying wall thickness while maintaining both mechanical performance and manufacturability.
Can Die Casting Handle Sudden Wall Thickness Changes?
Sudden changes in wall thickness are a common source of defects. Abrupt transitions can:
• Cause cold shuts due to interrupted metal flow
• Increase internal stress, making parts prone to cracks
• Create localized porosity or shrinkage cavities
Design best practices recommend smooth, gradual transitions—such as using tapers, fillets, and rounded features.
This reduces stress concentrations and ensures even cooling.
Collaborating with die casting experts can help avoid these pitfalls from the earliest design stages.
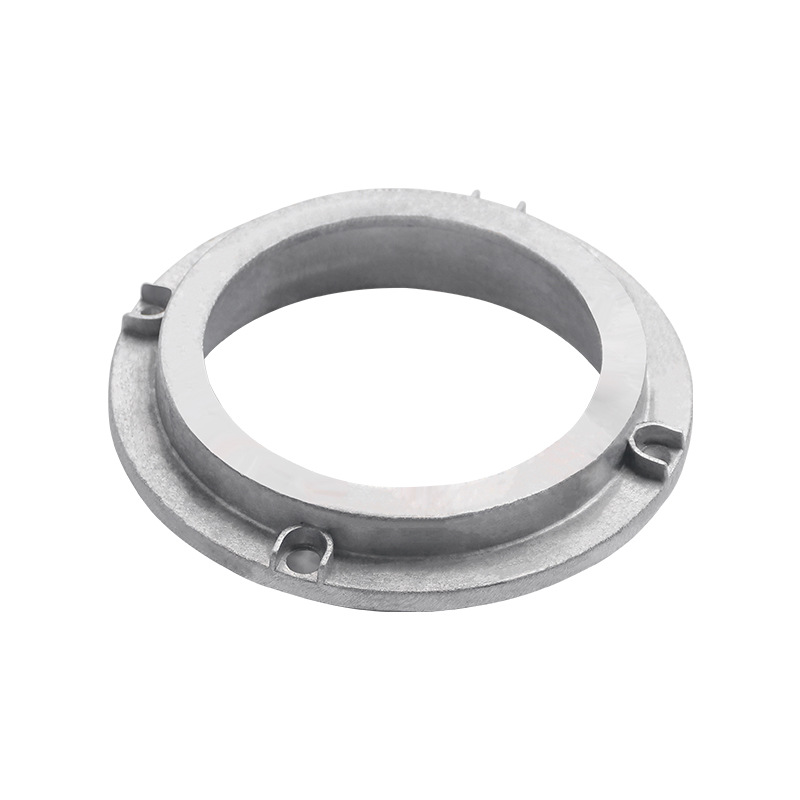
What Design Strategies Ensure Successful Thickness Variations?
Successful die casting with varying wall thickness relies on:
• Consistent draft angles to aid ejection and reduce sticking
• Optimized gate and runner placement to balance fill patterns
• Use of flow and thermal simulations to predict and solve issues
• Integration of structural ribs to maintain strength without adding unnecessary weight
Incorporating these elements into the initial design minimizes the risk of defects, shortens development time, and reduces manufacturing costs.
How Do Process Controls Support Quality in Parts with Varying Thickness?
Even the best designs can fail without robust process control. Manufacturers must:
• Control injection pressure and speed to avoid turbulence
• Maintain consistent die temperatures for balanced cooling
• Use real-time monitoring to detect deviations during production
These measures ensure that variations in wall thickness do not compromise structural integrity or appearance.
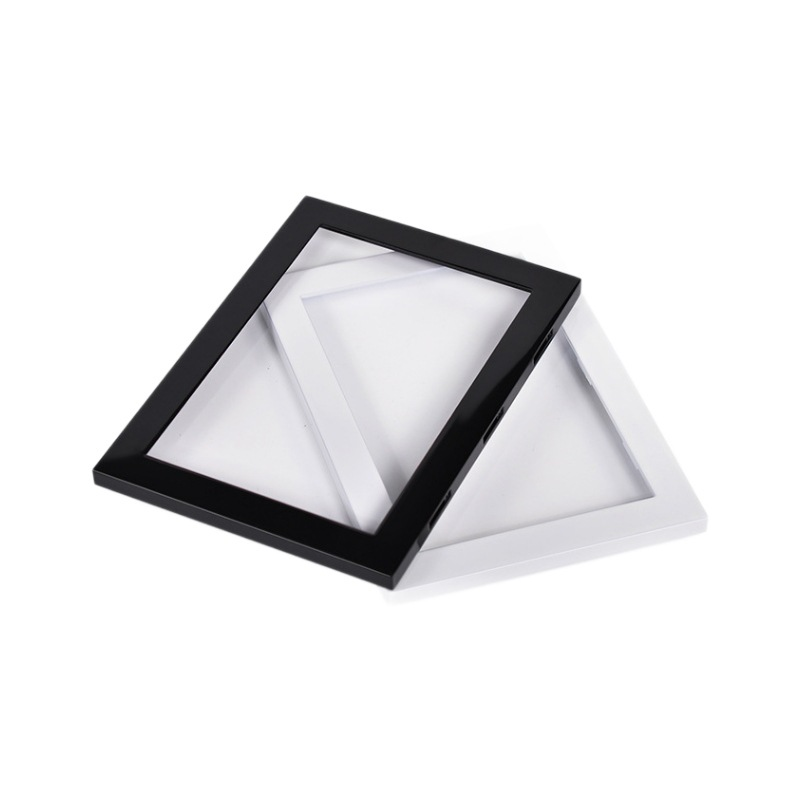
Conclusion:
Aluminium die casting can indeed accommodate varying wall thicknesses, provided that careful design principles and process controls are in place.
Gradual transitions, the strategic use of ribs and fillets, optimized gating, and balanced cooling systems all play a role in maintaining part quality.
While abrupt thickness changes invite defects such as shrinkage, warping, and porosity, these can be avoided through simulation-driven design and close collaboration with experienced manufacturers.
By working with trusted partners, engineers can bring innovative designs to life without sacrificing reliability, performance, or cost efficiency—ensuring every casting meets the highest standards from concept to production.