Ejector pin marks are one of the most common surface defects in aluminum die casting, often affecting both the visual appeal and functional integrity of the finished product.
These small circular indentations or blemishes, left behind when ejector pins push the solidified casting out of the mold, can compromise surface quality, increase the need for post-processing, and in some cases, even impact mechanical performance.
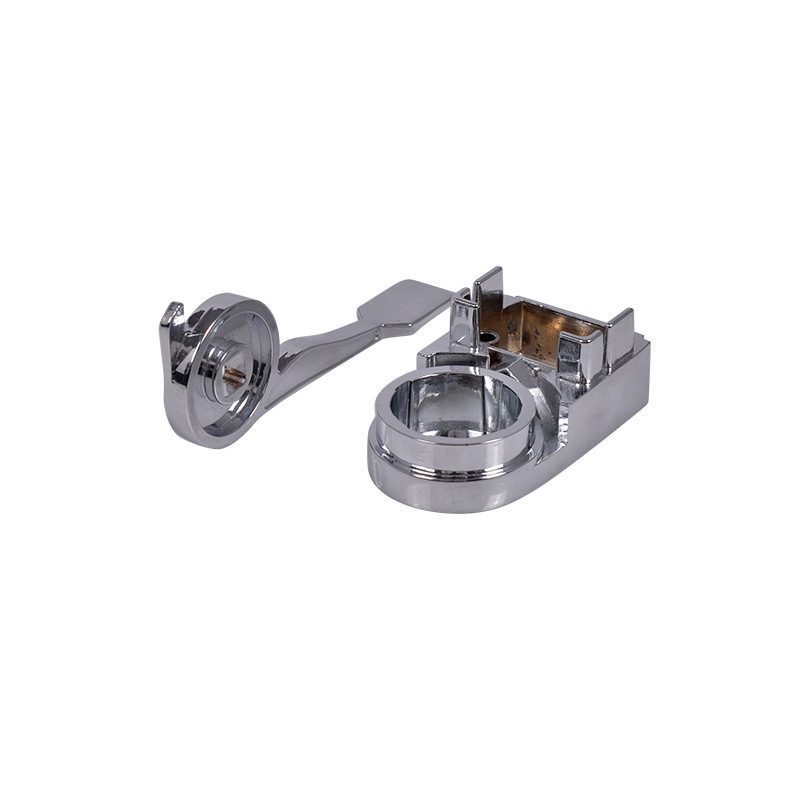
To prevent ejector pin marks in aluminum die casting, manufacturers must focus on optimizing mold design, controlling injection parameters, ensuring even cooling, and maintaining proper mold release.
A well-balanced approach that combines thoughtful die design with precise process control significantly reduces the risk of these defects and leads to higher-quality cast parts.
In the following sections, we’ll explore the main causes of ejector pin marks and examine practical design and process strategies to minimize or eliminate them, helping deliver superior die cast components consistently.
-
Table Of Contents
-
1. How Can Ejector Pin Marks Be Prevented in Aluminum Die Casting?
-
2. What Are Ejector Pin Marks in Aluminum Die Casting?
-
3. Why Do Ejector Pin Marks Occur?
-
4. How Does Mold Design Affect Ejector Pin Marks?
-
5. Why Are Draft Angles Crucial in Preventing Pin Marks?
-
6. How Can Injection Pressure and Speed Be Optimized?
-
7. What Role Does Cooling Play in Preventing Ejector Pin Marks?
-
8. How to Optimize Ejector Pin Layout and Diameter?
-
9. How to Address Ejector Pin Marks with Post-Processing?
-
10. Summary
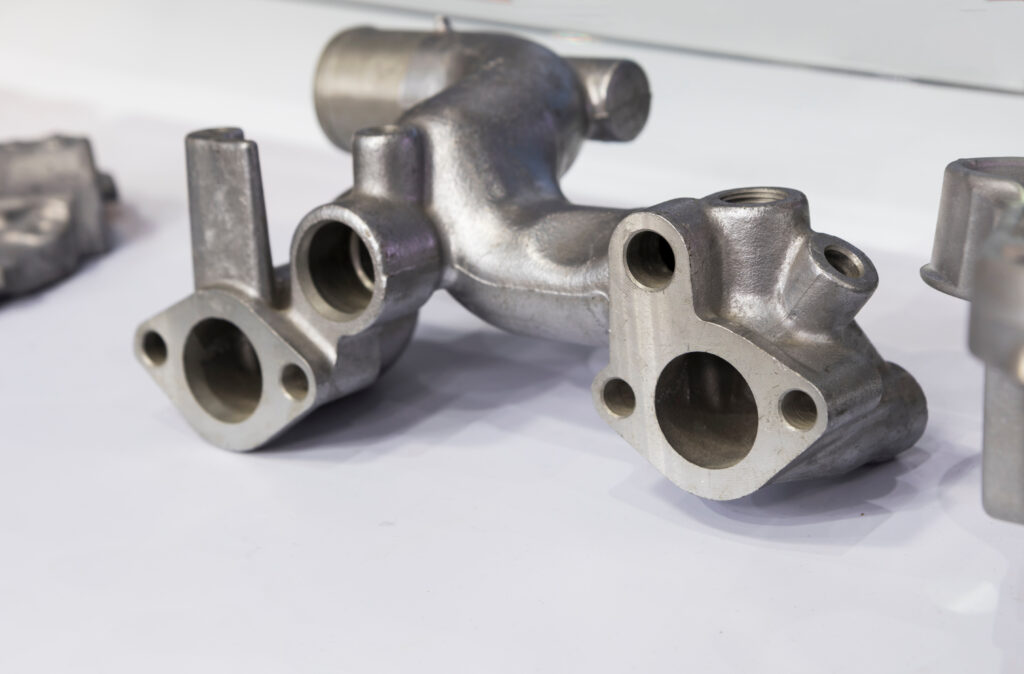
What Are Ejector Pin Marks in Aluminum Die Casting?
Ejector pin marks are the result of the mechanical force used to push solidified castings out of the mold.
These marks appear as small, often circular depressions where the pins made contact with the surface of the part.
While ejector pins are essential for automated die casting processes, poorly controlled ejection can leave visible flaws that not only affect the part’s appearance but may also lead to stress concentration points that weaken structural integrity.
The severity of ejector pin marks depends on factors such as the material being cast, part geometry, ejection force, and the precision of the mold design.
Addressing these factors early in the design phase is key to reducing defects.
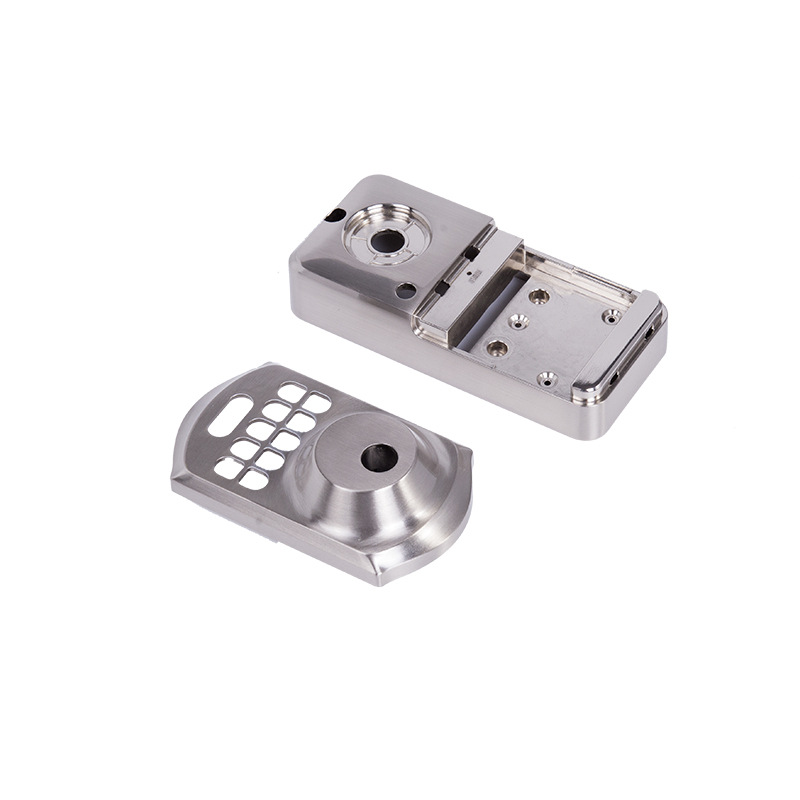
Why Do Ejector Pin Marks Occur?
Several factors can cause ejector pin marks in aluminum die casting.
Excessive ejection force, often due to inadequate draft angles or poor mold release, forces the pins to press harder against the casting surface, leaving deeper impressions.
Uneven cooling is another common cause, as it creates areas where the casting grips the die more tightly, requiring more force to eject.
In addition, high injection pressure or speed can push molten metal into small gaps around the ejector pins, causing flash or visible marks when the metal solidifies.
Finally, improper pin diameter or poor layout can concentrate stress in localized areas, making marks more prominent.
Understanding these root causes helps manufacturers address the issue holistically through design, process control, and maintenance.
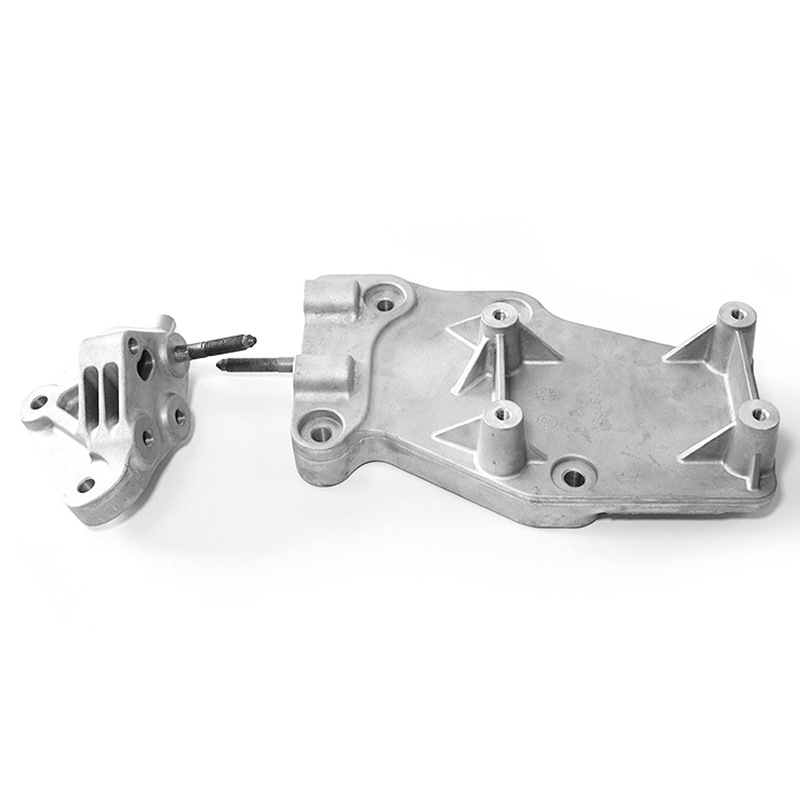
How Does Mold Design Affect Ejector Pin Marks?
Mold design is one of the most effective ways to prevent ejector pin marks.
The number, placement, and diameter of ejector pins should be carefully planned to distribute ejection forces evenly across the part.
Pins should be positioned away from highly visible or cosmetic surfaces whenever possible.
Using larger diameter pins helps distribute force over a wider area, reducing the risk of deep impressions.
Ensuring that ejector pins have smooth, polished surfaces also minimizes friction during ejection.
Proper clearance between the pins and the mold cavity is crucial to prevent metal from seeping into gaps, which can leave raised or sunken marks on the casting.
Why Are Draft Angles Crucial in Preventing Pin Marks?
Draft angles—slight tapers added to vertical surfaces of the mold—make it easier to eject the casting without excessive force.
Without adequate draft, parts tend to stick to the die walls, increasing the likelihood of ejector pin marks or even part distortion.
Applying consistent draft angles throughout the part reduces sticking, allows smoother ejection, and minimizes the force required.
Typically, draft angles of 1° to 3° are recommended, depending on the complexity of the part and the properties of the aluminum alloy used.
Early integration of draft considerations in the design stage is essential to reducing surface defects like pin marks.
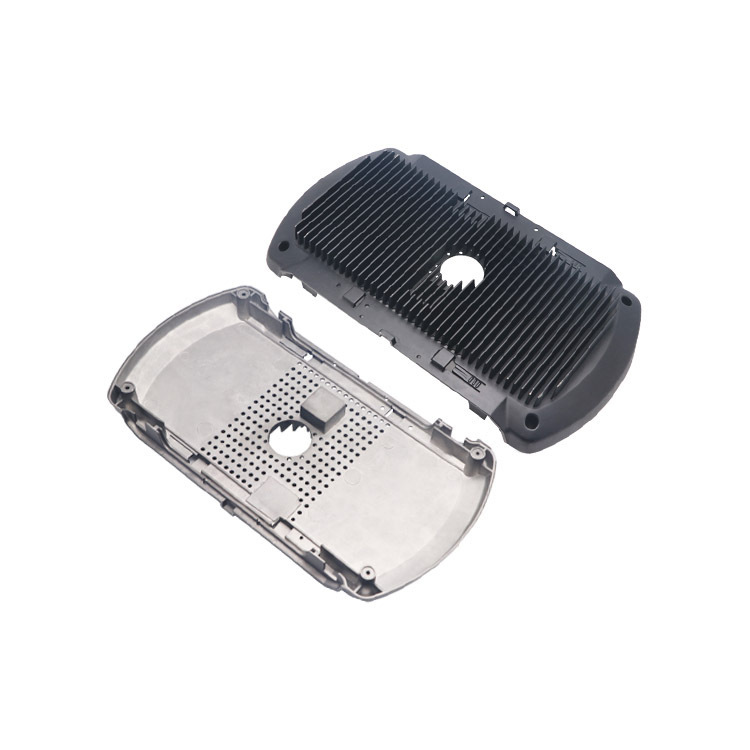
How Can Injection Pressure and Speed Be Optimized?
While high injection pressures and fast speeds are often necessary for filling complex molds, excessive values can lead to surface defects, including ejector pin marks.
Over-packing the mold increases internal stress and may force molten metal into pin clearances.
Optimizing injection involves balancing fill time, pressure, and speed to ensure complete cavity filling without creating unnecessary stress.
Multi-stage injection profiles can help—using higher speeds during initial fill and slower, more controlled pressure during the final stages.
Properly tuned injection parameters reduce the likelihood of parts sticking and improve overall surface finish.
What Role Does Cooling Play in Preventing Ejector Pin Marks?
Uniform cooling is fundamental to consistent solidification and smooth part ejection.
If different areas of the casting cool and shrink at different rates, the part can become distorted or stick unevenly, forcing the ejector pins to compensate with higher pressure—leading to marks.
Designing balanced cooling channels within the mold, targeting thicker or heat-retentive sections, and maintaining consistent die temperatures throughout the production cycle all help ensure even cooling.
By achieving uniform solidification, manufacturers can reduce internal stresses and the need for aggressive ejection, thereby minimizing defects.
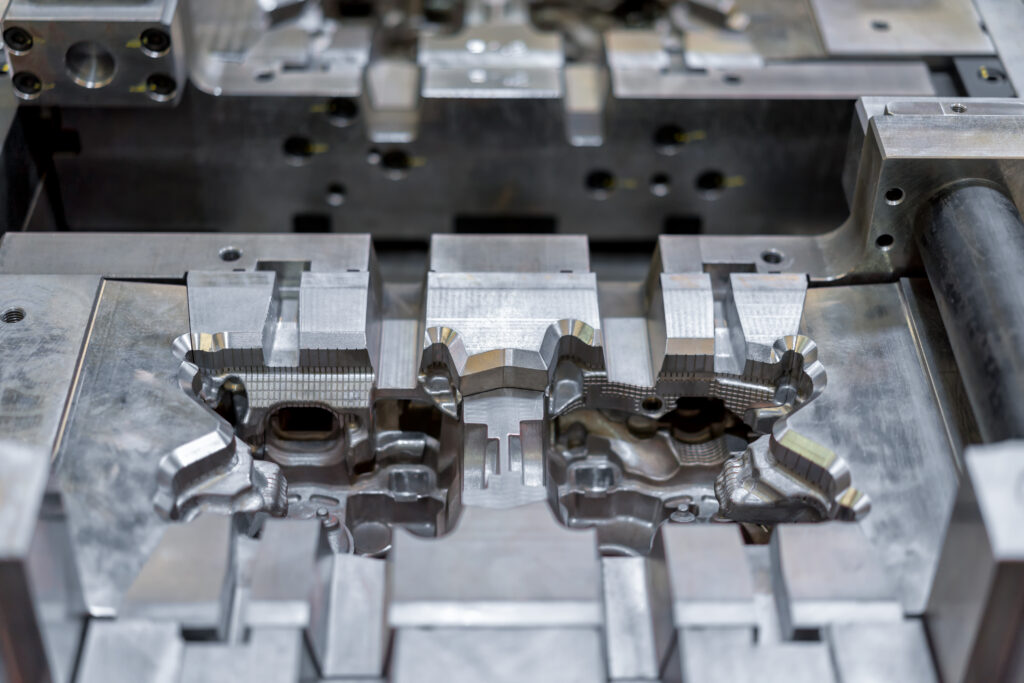
How to Optimize Ejector Pin Layout and Diameter?
The design of the ejector pin system—including both layout and pin size—plays a decisive role in defect prevention.
Strategically placing pins to apply balanced force across the part prevents localized pressure that could leave marks.
Where possible, larger diameter pins should be used to distribute force more broadly.
Additionally, ejector pins with slightly radiused or flat tips reduce stress concentration during ejection.
The choice of material and surface finish for the pins—typically polished and wear-resistant steel—also contributes to minimizing visible pin marks over the lifespan of the mold.
How to Address Ejector Pin Marks with Post-Processing?
In cases where minor ejector pin marks still occur, post-processing may be necessary to meet aesthetic or functional standards.
Light sanding, polishing, or machining can remove superficial marks.
Applying surface coatings such as anodizing or painting can also help mask minor imperfections.
While post-processing can be effective, it adds cost and time, making defect prevention through design and process optimization the preferred approach whenever possible.
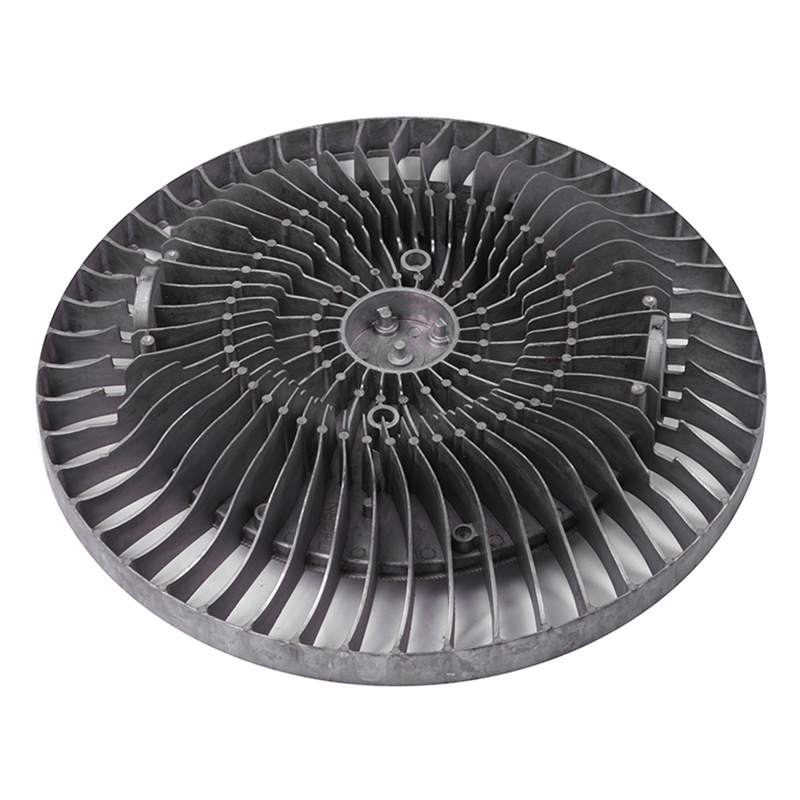
Conclusion:
Preventing ejector pin marks in aluminum die casting requires a holistic approach that combines thoughtful mold design, precise process control, and consistent maintenance.
By carefully optimizing ejector pin layout and diameter, incorporating appropriate draft angles, fine-tuning injection pressure and speed, and ensuring uniform cooling, manufacturers can significantly reduce the likelihood of ejector pin marks.
Advanced simulation tools can help identify and correct potential problem areas before production begins.
Through the integration of these best practices, die casting professionals can consistently deliver high-quality, blemish-free aluminum components, reducing rework, improving efficiency, and enhancing customer satisfaction.